In the precision-driven world of medical device manufacturing, material selection can make or break a product’s performance. Have you ever wondered how PA (Polyamide) and PVC (Polyvinyl Chloride) perform when subjected to CNC machining? These two materials, though commonly used, differ significantly in their machining behavior and end-use effectiveness. This article reveals how PA and PVC compare under CNC processing for medical applications, helping you make informed and confident material choices.
Executive Summary
Both PA and PVC are widely utilized in the production of medical equipment, thanks to their unique properties. PA is renowned for its high strength, wear resistance, and dimensional stability, while PVC stands out for its cost-effectiveness, chemical resistance, and ease of processing.
CNC machining, with its precision and repeatability, demands materials that can withstand high-speed tooling without compromising dimensional accuracy or surface finish. This article explores the core mechanical, thermal, and chemical characteristics of PA and PVC, and how these impact their CNC machinability and medical usability.
We will provide comprehensive data comparisons and detailed insights into performance factors such as precision, surface quality, biocompatibility, and long-term durability. Whether you’re developing surgical instruments, diagnostic tools, or implantable systems, this guide is designed to support your decision-making process.
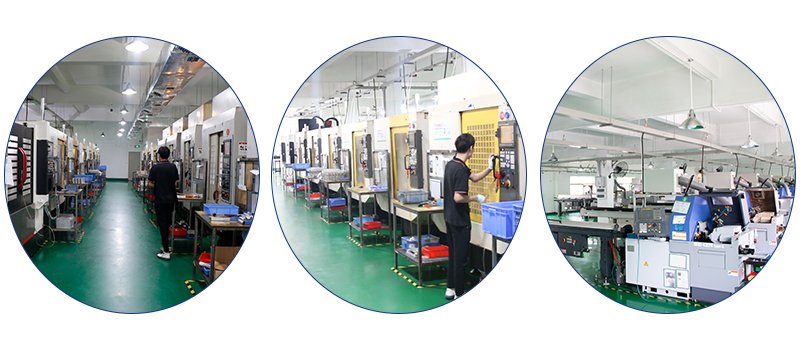
Transition Paragraph
In the sections that follow, we’ll dive into the technical profiles of PA and PVC, their behavior under CNC machining, and how they align with international medical-grade material requirements. Expect a clear, data-backed comparison that empowers you to choose the best-suited material for your CNC-machined medical components.
PA and PVC: Material Overview
PA (Polyamide), commonly known as nylon, is a semi-crystalline thermoplastic known for its high mechanical strength, low friction, and excellent wear resistance. It offers robust thermal stability, making it a strong candidate for components exposed to mechanical stress and fluctuating temperatures.
PVC (Polyvinyl Chloride), on the other hand, is an amorphous thermoplastic notable for its chemical resistance, low cost, and flame retardancy. It processes easily at lower temperatures and provides moderate mechanical strength, which suits less mechanically demanding applications.
In medical device manufacturing, PA is often used for parts requiring structural integrity and load-bearing capacity, such as catheter components and surgical tool housings. PVC finds its place in disposable devices like tubing, fluid containers, and enclosures due to its affordability and sterilization compatibility.
The Role of CNC Machining in Medical Device Manufacturing
CNC machining plays a pivotal role in producing high-precision medical components with tight tolerances and consistent repeatability. Its computer-controlled nature allows for the creation of complex geometries that are difficult to achieve with molding or casting techniques.
Medical-grade materials must endure high-speed cutting tools while maintaining dimensional integrity and biocompatibility. CNC technology is often employed for producing customized implants, surgical guides, housings for electronic diagnostics, and other patient-critical components. The process also supports rapid prototyping and short production runs, reducing time to market.
Material response to CNC machining directly impacts production efficiency, product quality, and regulatory compliance. Therefore, understanding how PA and PVC behave under CNC processing is crucial to choosing the optimal material.
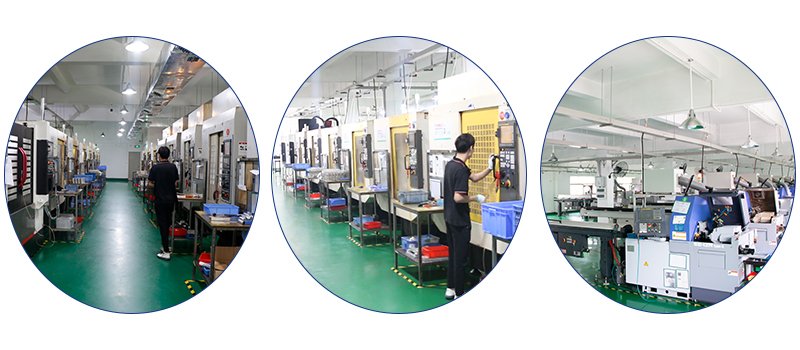
CNC Machining Performance of PA
PA excels in CNC machining due to its toughness, high melting point (approximately 220°C), and excellent abrasion resistance. It machines cleanly, with minimal burring and deformation, even under high-speed cutting. Its natural lubricity also reduces tool wear, extending the lifespan of cutting instruments.
Dimensional accuracy with PA is consistently high, although moisture absorption can slightly affect tolerances post-machining. When dried properly before processing, PA can maintain precision even in tight-tolerance medical applications.
Additionally, PA offers good thermal stability during machining, resisting melting and warping under heat generated by cutting tools. This stability makes it suitable for parts requiring complex features and smooth surface finishes.
However, PA can be prone to shrinkage and may require annealing to relieve internal stress after machining. Overall, its machining behavior makes it ideal for precision parts in load-bearing or friction-sensitive environments.
CNC Machining Performance of PVC
PVC is favored for its excellent machinability at lower tool spee可以
你去给他们ds and reduced thermal thresholds. It softens around 100°C, which allows for easy material removal but necessitates careful temperature control during CNC machining to avoid melting or chipping.
One of PVC’s strengths is its ability to deliver consistent surface finishes with minimal post-processing. Its rigidity provides clean cuts, though it’s more brittle than PA, which may limit its use in parts requiring impact resistance.
PVC is also cost-effective, both in material cost and machining time. Its machinability leads to shorter cycle times and reduced tool wear when processed under the correct conditions. This makes it particularly suitable for disposable or non-load-bearing medical components.
In terms of safety, chlorine gas release from machining PVC requires effective dust extraction and ventilation. When managed properly, however, PVC offers a highly efficient route to producing low-cost, high-volume components.
PA vs. PVC: Precision and Surface Quality Comparison
Property | PA (Polyamide) | PVC (Polyvinyl Chloride) |
---|---|---|
Machining Precision | High | Moderate |
Surface Finish Quality | Excellent with minimal burring | Good with careful thermal control |
Tool Wear | Low | Moderate |
Heat Resistance | High | Low |
Post-Processing Need | Medium (possible annealing) | Low |
Moisture Sensitivity | Yes | No |
When comparing PA and PVC in terms of CNC-machined precision and finish, PA generally offers better tolerance control and smoother results, especially under mechanical stress. PVC, while offering good surface finishes, is less suited to fine-detailed features or parts exposed to long-term mechanical forces.
The table above outlines the core performance metrics that differentiate the two materials. Designers focused on performance and precision may lean toward PA, while those prioritizing cost and speed may find PVC a more attractive choice.
Biocompatibility and Long-Term Stability Considerations
Biocompatibility is critical in any medical application. PA is often chosen for implantable and internal-use devices due to its lower cytotoxicity and stable long-term behavior. It is also resistant to most sterilization methods, including autoclaving and ethylene oxide treatment.
PVC, though biocompatible for many external or single-use applications, may raise concerns due to additives like plasticizers, which can leach over time. While medical-grade PVC formulations are available, they often undergo stricter compliance testing to ensure safety.
In terms of aging and degradation, PA resists UV and environmental stress cracking better than PVC. It is generally preferred for reusable instruments and long-life applications. PVC, while stable under controlled conditions, may become brittle or discolor with prolonged exposure to light or sterilization.
Both materials are used globally in regulated markets, but PA often meets higher-grade certifications for critical applications.
Region | Biocompatibility Requirement (Summary) |
---|---|
USA (FDA) | USP Class VI, ISO 10993 required |
EU (MDR) | Requires CE marking and ISO 13485 compliance |
Japan | Follows PMDA standards and ISO 10993 |
China | CFDA registration and GB/T standards |
Choosing the Right Material: A Decision Guide
Selecting between PA and PVC for CNC machining in medical devices depends on a combination of performance criteria, cost considerations, and regulatory requirements. Here’s a quick guide:
Choose PA if:
High mechanical strength is needed
The component is reusable or subject to sterilization
Dimensional accuracy is critical
Surface quality and wear resistance are top priorities
Choose PVC if:
The part is disposable
Cost efficiency and short production time are crucial
Sterilization requirements are moderate
The component is not mechanically stressed
Additionally, consider post-machining processes, storage conditions, and long-term behavior. Collaborate with your CNC machining partner to conduct prototype runs and test samples under real-use conditions.
FAQs
What are the key differences between PA and PVC in CNC machining?
PA offers superior precision, thermal resistance, and mechanical durability, making it ideal for demanding applications. PVC, in contrast, provides good surface finishes at lower costs and is easier to machine but is less resistant to heat and mechanical stress.
How do I choose the right material based on my device’s needs?
Consider the device’s function, expected lifespan, regulatory requirements, and processing conditions. If your product is a reusable surgical tool, PA may be ideal. For disposable components or fluid systems, PVC is often more practical.
How do CNC machining trends affect material selection?
Modern CNC machines offer improved thermal management, adaptive tooling speeds, and advanced simulation. These enhancements allow materials like PVC to be machined more precisely and reduce tool stress when machining harder materials like PA. However, material properties still govern the ultimate choice.