Introduction: Choosing the Right CNC Material is More Than Just a Detail
CNC machining has revolutionized modern manufacturing with its ability to deliver high-precision components across industries. But at the heart of every successful CNC project lies a critical decision—the choice of material. Among the most widely used CNC machining materials are aluminum, stainless steel, and titanium—each with unique properties that influence performance, cost, and application. This article explores how to choose the right material for your CNC project by comparing these three powerhouse materials in terms of strength, machinability, cost, and suitability across sectors.
Quick Summary: Which CNC Material Is Best for You?
Whether you’re designing aerospace components, consumer electronics, or medical equipment, material selection plays a decisive role in CNC machining success.
Aluminum is lightweight, highly machinable, and ideal for high-speed production, making it a go-to for automotive and electronics industries.
Stainless steel boasts exceptional corrosion resistance and strength, suited for harsh environments and structural applications.
Titanium delivers the highest strength-to-weight ratio, perfect for aerospace and medical implants—but comes at a higher cost and greater machining difficulty.
This article breaks down the physical properties, corrosion resistance, machining complexity, cost-benefit ratios, and global preferences to guide you in selecting the optimal CNC material for your specific needs.
From Design to Execution: Why Material Selection Matters in CNC Machining
The choice between aluminum, stainless steel, and titanium isn’t just technical—it affects project timelines, costs, and end-use performance. As each material has distinct characteristics, selecting the right one can boost efficiency, improve durability, and enhance your product’s market success. In the following sections, we’ll examine these three materials in depth and offer actionable guidance based on technical parameters and real-world applications.
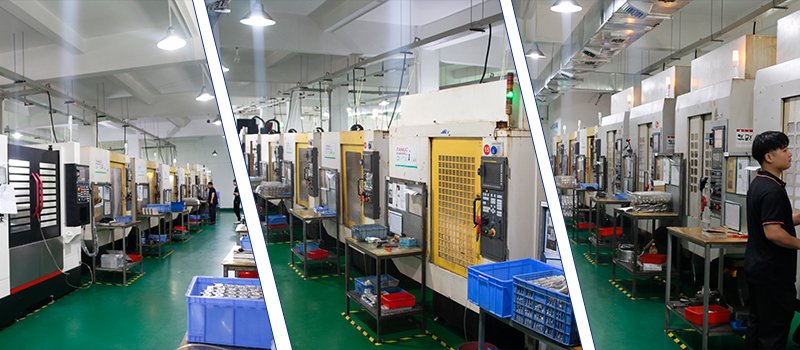
Aluminum and CNC: Lightweight Versatility in Action
Aluminum is one of the most popular choices in CNC machining due to its favorable strength-to-weight ratio, outstanding machinability, and excellent thermal and electrical conductivity. Grades like 6061-T6 and 7075 are common in everything from consumer electronics to automotive parts.
Physical Characteristics: Aluminum is soft and ductile, which allows for high-speed machining and low tool wear.
Machinability: It offers clean, burr-free edges and tolerates tight tolerances without complex setups.
Applications: Common in automotive, aerospace interiors, robotics, and custom prototypes.
Environmental Resistance: While not as corrosion-resistant as stainless steel or titanium, aluminum can be anodized to improve durability and wear resistance.
For projects requiring rapid turnaround and low weight, aluminum is often the most cost-effective solution in CNC machining.
Stainless Steel: The Corrosion-Resistant Workhorse of CNC Machining
Stainless steel is prized in CNC machining for its strength, durability, and resistance to rust and corrosion, making it an ideal candidate for medical instruments, structural parts, and marine equipment.
Grades & Types: Popular options include 304, 316, and 17-4PH, each with specific mechanical and corrosion-resistant properties.
Machining Challenges: Stainless steel’s hardness can lead to faster tool wear and slower cycle times, but modern carbide tooling and optimized feed rates can mitigate this.
Heat Resistance: It maintains mechanical integrity at elevated temperatures—vital for engine and industrial applications.
Applications: Found in food processing, chemical manufacturing, architecture, and heavy-duty enclosures.
Though more challenging to machine, stainless steel is invaluable where durability and corrosion resistance are non-negotiable.
Titanium Alloys: Where Strength Meets Precision in CNC Machining
Titanium stands out with its superior strength-to-weight ratio, making it a premium choice in aerospace, medical, and military applications. Its biocompatibility also makes it ideal for surgical tools and implants.
Mechanical Strength: Titanium can match or exceed the strength of stainless steel at nearly half the weight.
Corrosion Resistance: Excellent resistance to chemicals and saltwater environments.
Machining Considerations: Difficult to cut due to its low thermal conductivity and high toughness; requires specialized tooling, slower speeds, and coolant-intensive processes.
Applications: Critical in aircraft engine parts, orthopedic implants, high-performance motorsports.
Despite its machining challenges, titanium is unmatched when performance and reliability are paramount.
Cost Analysis: Balancing Performance and Budget
Material | Raw Material Cost | Machining Difficulty | Tool Wear Rate | Overall Cost |
---|---|---|---|---|
Aluminum | Low | Easy | Low | Low |
Stainless Steel | Moderate | Moderate | Medium | Moderate |
Titanium | High | Difficult | High | High |
When budget constraints exist, aluminum offers the best cost-efficiency, while stainless steel provides a balance between strength and price. Titanium is best reserved for high-value applications that justify the higher costs of machining and tooling.
Cultural and Regional Influences on CNC Material Selection
Material preferences in CNC machining aren’t universal. In North America and Europe, titanium sees widespread use in aerospace and medical sectors. Asian manufacturers, particularly in Japan and South Korea, favor stainless steel for its structural versatility and hygiene standards.
Supply Chain Considerations: Aluminum enjoys a stable global supply chain, while titanium prices fluctuate with aerospace demand.
Cultural Preferences: Western markets often emphasize lightweight innovation (favoring aluminum/titanium), while industrial economies in Asia may prioritize cost and durability.
Understanding these differences can help businesses navigate global manufacturing partnerships more effectively.
Technical Guide: Matching CNC Materials to Project Requirements
Material | Best For | Avoid When |
---|---|---|
Aluminum | Lightweight parts, fast prototyping | High-strength/high-temperature needs |
Stainless Steel | Corrosive environments, strength-critical use | High-speed or lightweight applications |
Titanium | Aerospace, medical, premium products | Budget-sensitive, high-volume production |
Machining Parameters: Titanium needs lower feed rates and coolant-rich setups; aluminum allows high-speed milling; stainless steel requires balanced speed-to-torque tooling.
Case Study: A medical device company chose grade 5 titanium over stainless steel to reduce implant weight by 40%, despite longer machining time.
Matching CNC machining parameters to material capabilities ensures reliability, cost-effectiveness, and regulatory compliance.
CNC Material Selection Through a Global Lens
The rise of online CNC platforms and distributed manufacturing has introduced new dimensions to material sourcing and standardization. More companies now leverage AI-driven material selection tools, optimizing based on geometry, tolerances, and environmental exposure.
Global Trends: Demand for sustainable materials and lighter alloys continues to grow.
Digital Solutions: Platforms like Xometry and Fictiv allow global customers to pre-select materials and see cost implications instantly.
Material selection is no longer isolated—it’s influenced by cross-border regulations, logistics, and design ecosystems.
FAQs: CNC Material Selection Explained
Q1: What are the main differences in CNC use between aluminum, stainless steel, and titanium?
A: Aluminum is best for lightweight, cost-effective parts; stainless steel excels in corrosive and structural applications; titanium is for high-performance, low-weight demands.
Q2: What if I’m on a tight budget—what CNC material should I choose?
A: Aluminum is the most affordable. If strength is needed, 304 stainless steel is a solid mid-cost alternative. Avoid titanium unless absolutely necessary.
Q3: Do cultural preferences affect CNC material choices?
A: Yes. Western countries often favor titanium for innovation, while Asian manufacturers lean toward stainless steel due to infrastructure and durability needs.