9 quality control processes
CNC Machining customization Process From raw materials to cnc machining finished product shipping process
From material testing to product packaging and delivery, we achieve efficient optimization of the entire process through customized CNC machining, program optimization, quality control and surface treatment.
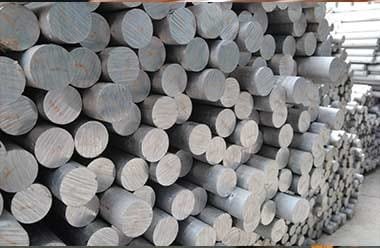
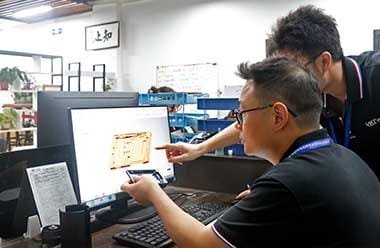
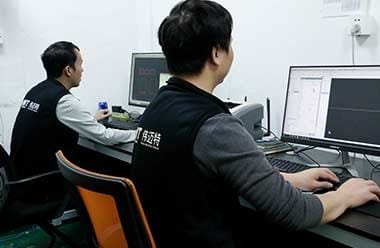
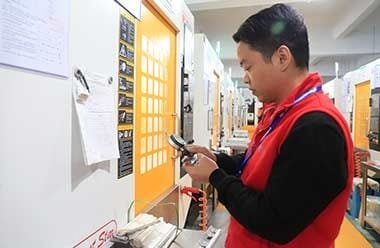
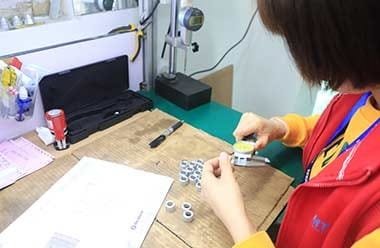
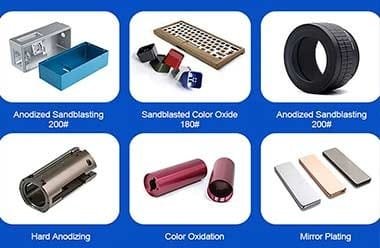
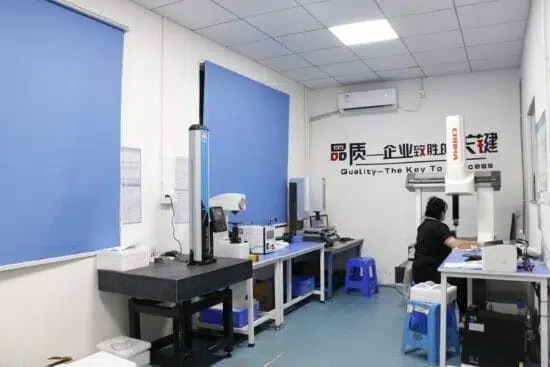
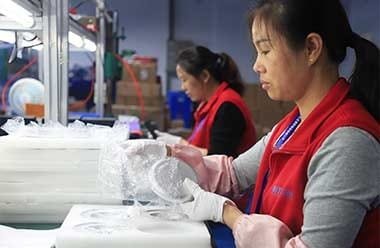
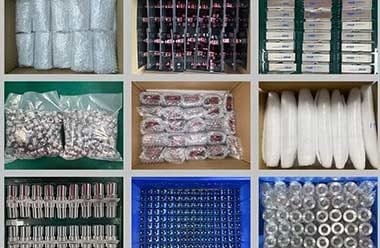